Concrete paving bricks are widely used as a decorative paving element. Its production technologies go back decades and are relatively conservative, that is, they have not undergone significant changes recently. World standards define numerous parameters of paving slabs that guarantee their reliability and durability. However, there is still no single standard that would objectively regulate the key aesthetic characteristic of the coating – the color of the face layer.
In modern practice, color assessment usually comes down to a subjective requirement: “the color must correspond to the manufacturer’s standard.” But what exactly is meant by “standard”? Do all manufacturers have it, and is it defined the same? Are the standards the same at different plants of the same manufacturer? How and by whom is the finished product compared with this standard? These questions are relevant even for simple monochrome colors (yellow, red, etc.), and when making products with a mixture of colors, their importance increases many times over.
In this article, we propose an approach to determining the objective parameters of the color of paving slabs and consider the following questions:
● How to describe a color to fix it as a standard?
● How to control whether the resulting color matches the selected standard?
Requirements for measuring equipment
Since the purpose of the research is objective parameters, a means of measuring these parameters is needed that works according to a clear methodology. The key element of the proposed color control system is a computer vision complex that will analyze products both immediately after pressing (on the “wet side”) and after curing (on the “dry side”). The system must guarantee high-quality images of the entire pallet of products without color or illumination distortion. If there are local features of the installation site (type of lighting, background, reflections), they must be compensated in hardware or software so that the final image is uniform and normalized. It is important to ensure that installations are calibrated to obtain consistent data not only across different installations within the same plant, but also across different plants of the same manufacturer.
Preparing a color reference
In any production, a qualified quality manager can identify product samples that are considered typical representatives of the desired color scheme. From this point, the preparation of a standard for the system begins: the “marking” of samples selected as reference takes place.
To turn a set of reference samples into a digital master, it is necessary to identify key parameters that are understandable to both humans and the computer vision system. The main stages of preparing a color standard are as follows:
1. Selection of reference samples: A qualified quality specialist manually selects representatives of each required color.
2. Bringing out pure colors: the software system, knowing that the face layer consists of one or more color components, analyzes the image and selects individual “pure” colors, the mixing of which occurs in the texture layer. It is important to process the entire analyzed product molding field as a single space, otherwise the same colors on different molds will have different statistical characteristics.
3. Definition of statistical parameters: for each selected pure color, its quantitative share in the texture layer is calculated, as well as the characteristic sizes of color zones. As a result of processing reference samples for each color, a set of parameters is formed that sufficiently fully describes the standard:
● RGB codes of “pure” basic colors;
● The percentage of each pure color in the image;
● The characteristic size of color zones and their coverage of the image area, describing the pattern of color mixing.
The physical meaning of the first two parameters is clear from the name. The latter is worth explaining separately. In the color pattern within the molding zone, closed zones of similar colors can be distinguished. The size and shape of these zones depends on the color mixing pattern. This parameter - the characteristic size of color zones indicates what size zone is characteristic of a given color - occupies more than 50% of the color coverage area. For versatility, let’s take the value of this parameter not in absolute values, but as a percentage of the entire visible molding zone. This raises the requirement for color analysis of the entire molding zone without taking into account the boundaries between stones, otherwise the statistical parameters of one color will depend on the shape, which is incorrect.
Thus all parameters satisfy the requirement of objective measurability and clarity for human perception.
The mono color standard in general has the value of the color content parameters in the face layer of 100%, and the standard is reduced to the RGB color code. In the case of a colormix product, all three groups of parameters are key to describing the color. An illustration of automatic calculation of the standard for a colormix color looks like this:
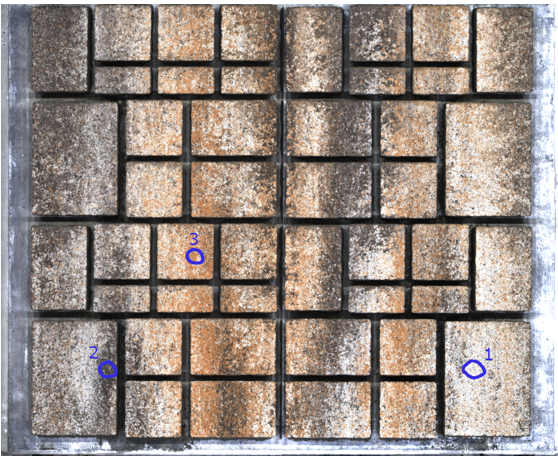
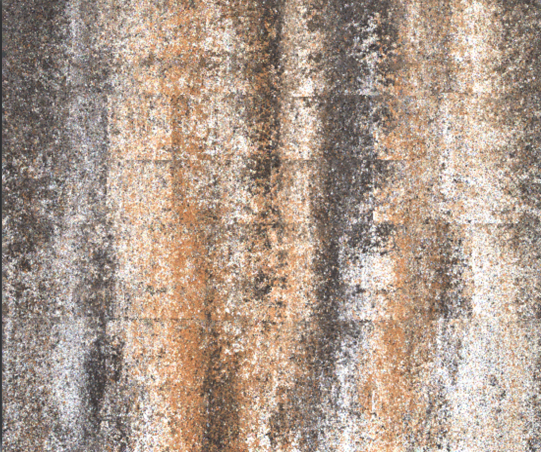
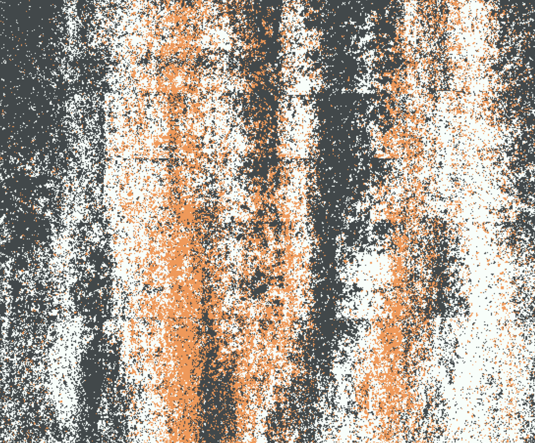
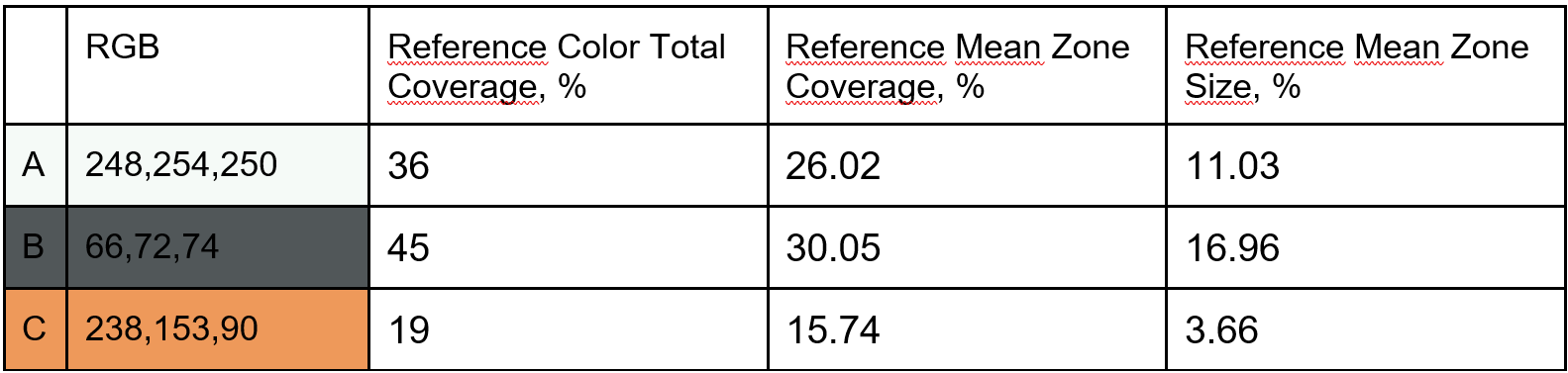
Taking into account the specifics of the plant
The color standard is a key parameter for subsequent control. However, in addition to the standard, the local characteristics of each production should also be taken into account. The quality manager must reflect these features in the system settings. To build a full-fledged analytical model you need:
1. Set tolerances for parameter deviations: Requirements for color stability and uniformity of color components may differ in different factories. The limits of permissible deviations depend on these criteria.
2. Configure color conversion between wet and dry sides: the color of the surface after pressing (“wet side”) and after curing (“dry side”) can vary significantly. It is advisable to perform this nonlinear transformation using machine learning methods, using real data from a specific plant and a specific composition of the concrete mixture. The system, trained on reference data, will be able to predict the color of the product on the “dry” side based on the image of the “wet” side.
Control of color compliance with the standard
A prepared standard is an objective description of a color sufficient for its monitoring. Let us note once again that color monitoring is important at all stages of the technological process: on the wet side to influence the production process and adjust technological production parameters in a timely manner, on the dry side to assess the final quality of the finished product and rejection.
Previously, we formulated the concept of a color standard as a set of three groups of parameters: the value of the color code in the RGB space, the colors proportion, and the characteristic size of the colors zone. Monitoring compliance with the standard implies monitoring the compliance of all given parameters. Due to their large number, a simple visualization for this task has yet to be developed. Here we will give several examples to illustrate the consistency of the selected parameters.
Example for monocolor
In the case of monocolor, the only control parameter is the color code in RGB or another color space. The difference between the observed color vector and the reference value can be converted into a single number (modulus) and plotted. Below is a practical example of the dynamics of this parameter in production. The graph shows how, with the next batch of concrete mixture, a shade is obtained that differs from the previous one within the batch.
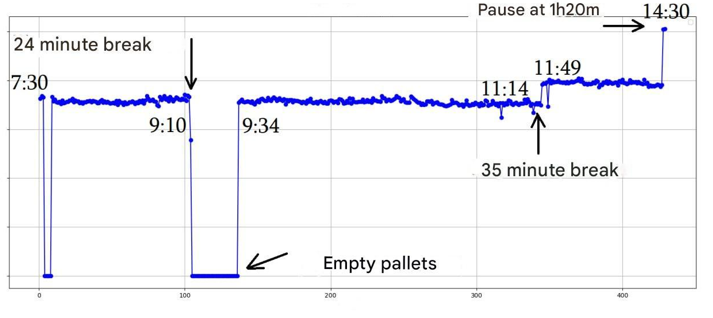
Example for colormix
In the case of having several colors to control, the hue parameter of each color component becomes less significant than in the case of a monocolor. For such products it is more important to control proportions of color components and characteristic sizes of zones, which we will illustrate in this example.
An example for a color mix close to the standard and a color with unacceptable deviations:
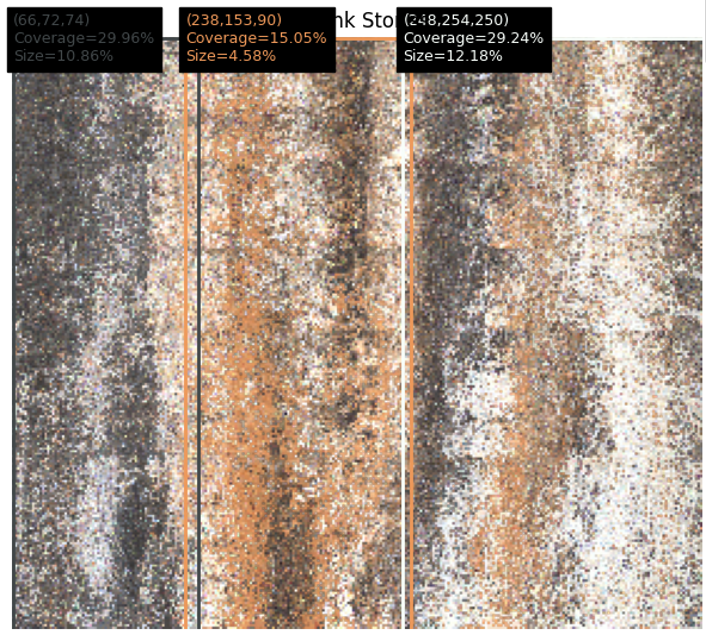
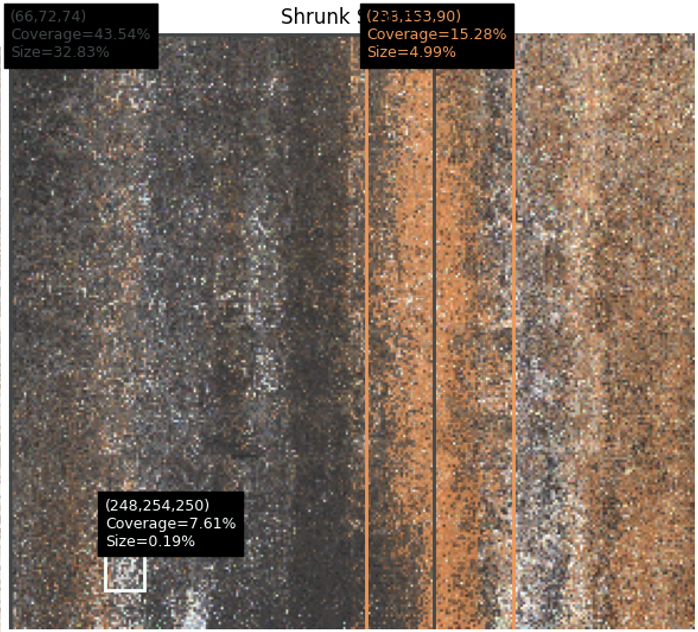
In the table and graph you can see the difference between the parameters of the presented example and the reference ones. A graph of the key parameters of color components for 10 examples of normal pallets and one defective one is also presented; it is clearly seen that the spread of parameters obeys a statistical pattern.
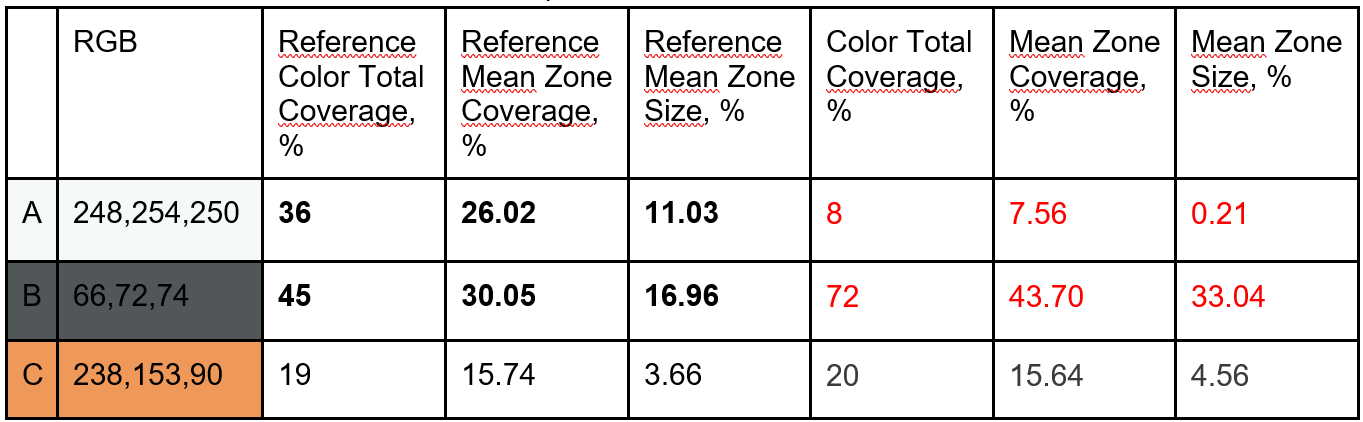
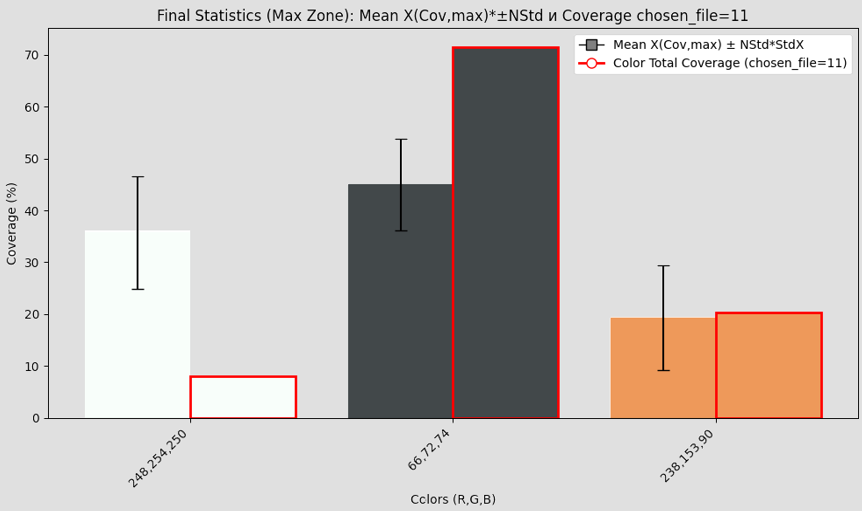
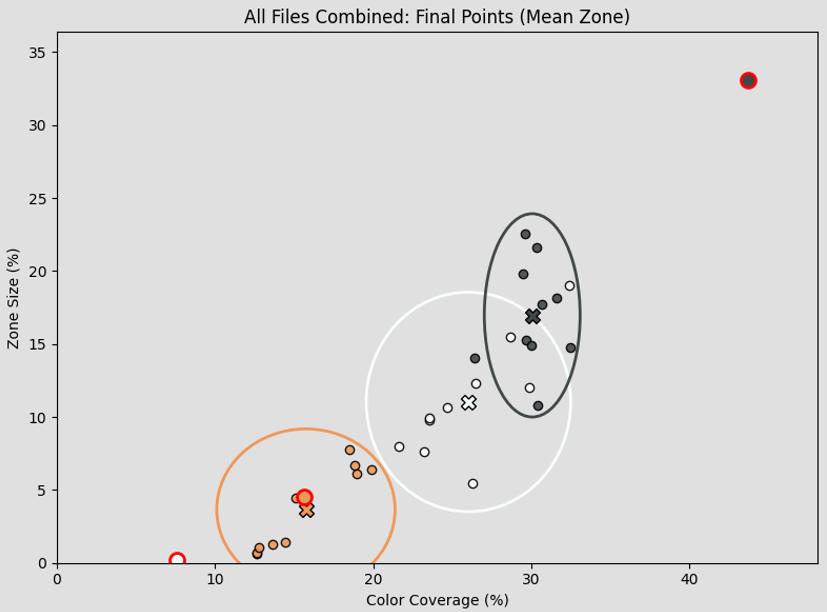
Color control on wet and dry sides
It is important to consider that color standards are usually established for finished products (dry side), while operational color control is preferably carried out immediately after molding (wet side). This allows you to timely adjust the recipe if deviations occur. To do this, the system must perform a two-way conversion of color parameters between wet-side and dry-side states. It should be noted that this transformation affects the shades and has almost no effect on the proportions of colors. Thus, we can conclude that shade control, which is more important for mono colors, is more susceptible to inaccuracies in the wet-to-dry conversion. At the same time, for determining the proportions and mixtures of color mixes, this factor is less important and can be assessed even without a clear wet-dry color conversion.
Conclusion
Despite the obvious importance of such a parameter as the color of paving, the procedure for its instrumental control has not yet become a standard in the industry. The main reason is the technical complexity and novelty of methods for continuous monitoring of color parameters. Only in recent years has equipment appeared on the market that allows automatic and systematic recording and analysis of product color directly on the conveyor, such as QuatroPBC from Quatromatic.
This article proposes objective parameters for describing both simple and complex (color mix) color solutions. As technology develops and uniform industry traditions and standards emerge, this set of parameters will be refined and supplemented. But now, with their help, it is possible to standardize color parameters both at a single plant and between plants of the same manufacturer.